We are currently implementing a Safety and Environment management system with the aim of certifying the ISO 45001 for Safety and Health at Work and ISO 14001 for Environment Standards.
This plant opened September 2008 and manages sewage effluents. To control this effluent, a measurement and analysis system was established through an environmental analysis laboratory certified by ISO 17001 and authorized by OPDS and ACUMAR.
The foundry has underground water extraction wells and analysis wells on the water table (phreameter). Controlled by a geologist 4 times a year. Water wells are chemically and bacteriological controlled. In addition, a flow meter was installed in each well in order to know the water consumption in our production processes.
Special waste is stored in a conditioned area according to the guidelines established by Resolution 177 – E / 2017 of the MINISTRY OF ENVIRONMENT AND SUSTAINABLE DEVELOPMENT.
This system was implemented to reduce the handling of chemical products by personnel. Nowadays, they are automatically mixed by equipment specially designed to do so, with no direct contact required.
Starting in 2008, a more exhaustive management of the discarded sand was started. We went from there being 70 tons of sand discarded, to it now only being only 6 to 10 tons. This was due to the investment in the sand recycling system (Shake Out). Regarding the purpose, several alternatives were developed, among which we can mention: incorporation of sand into the clinkering for cement manufacturing in Loma Negra, concrete blocks, ceramic manufacturing, etc.
From 2008 to date, diffuse emissions have been channeled through chimneys, improving effluent quality controls. We have a schedule of operational controls with specific testing frequencies. Sleeve filters were incorporated in various factory production areas.
There is also an ongoing plan to install opacity meters in chimneys.
Domestic waste is separated from the special waste, monitoring its evolution through specific KPIs. Lastly, and thanks to the separation of paper, we collaborate with the Garrahan Foundation.
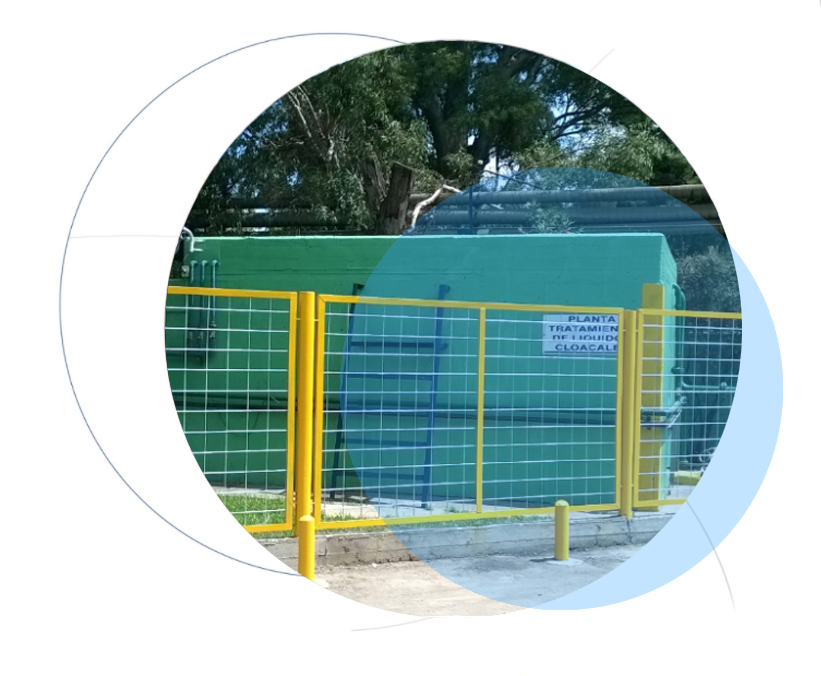
ENVIRONMENTAL MANAGEMENT
The activities developed in FSC are committed to implement management policies oriented towards the preservation and care of the environment, seeking to achieve sustainability in the operations carried out, such as:
By applying the 3R concept, we reuse the chips generated in the machining area in our production processes; scrap metals; pieces that are returned by our customers after the end of their life cycle; ingots etc.
Through the incorporation of mechanical and thermal technology, we managed to recover the discarded sand, considerably bringing down the environmental impact on river beds by reducing extractive activity.
We have developed an environmental monitoring program based on environmental aspects and impacts generated by our operations, such as air quality, quality of discharge of liquid effluents, control of underground water resources and solid matrices, such as sand and slag.
The legal requirements established by the environmental regulation entities, at the District, State and National levels, are complied with. FSC has Environmental Certificates, Qualifications and Permits necessary for its normal operation.
Based on practices with the purpose to manage our activities in an environmentally friendly manner, we train staff permanently, promoting the concept of the 3Rs through staff training sessions.
The influence of the greenhouse gas (GHG) emissions on the phenomenon of climate change, and the growing concern about energy scarcity, is globally recognized. Consequently, FSC, committed to caring for the environment by uses a high percentage of energy from renewable sources in its production processes.
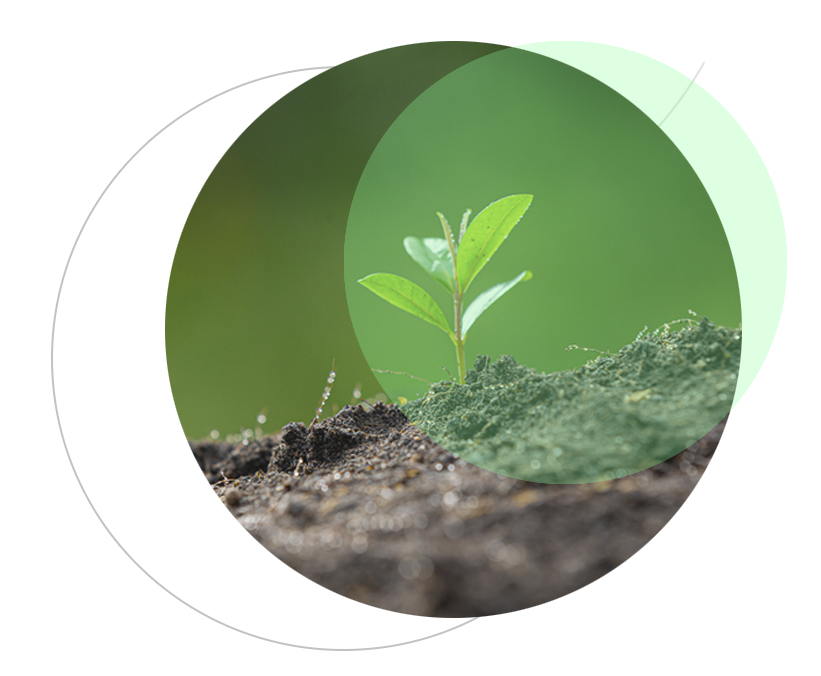